Don't settle for an out-of-the-box solution to your prepress workflow problems.
Let frozentraffic custom design a solution that fits you to a tee.
We’ll pick you up where Whitepapers left you off.
When it comes to prepress departments, there are no one-size-fits-all solutions. Every company is different, and every job has its own peculiarities. Trying to connect a ERP/MIS and prepress workflow system out of the box is like opening a package that doesn’t have all the parts you need inside.
That’s where frozentraffic comes in. Frozentraffic helps companies configure their order management and workflow systems for the specific needs of their prepress departments.
Here’s an example. You have a customer who used to order a year’s supply of labels oncek every twelve months. Now they’ve gone to the Just In Time system, and they order in smaller batches, twelve times a year. So, your pre-press department is doing setup work twelve times a year for the same price as they did for one order once a year. In So, the company buys a fancy new order management system and sets it up with the help of the seller’s whitepaper. But because the whitepaper can’t explain all the ways the system can be modified for this particular company, there are inefficiencies that result in delayed orders, production snafus, and other problems, and the system doesn’t work as well as it was designed to do. Frozentraffic can fix all that.
Our CEO Robert Kohl has more than twenty years’ experience in the printing industry, working for industry leaders like Agfa, Kodak and Esko, among others, and he knows how to get the most efficiency and productivity out of a prepress department. He is an expert in digital workflow systems for the printing industry, and he knows how to work with your engineers and technical people to configure these complex systems so they are perfectly tailored to your specific needs.
What is our focus?
Optimizing the ERP/MIS prepress connection
Automating the prepress process
We help you automate recurring prepress tasks by integrating ERP data successfully.
Integrating production
We optimize your production through target-oriented and comprehensive integration of print and ERP data.
How do we work?
01
Analyze your workflow and establish goals. We do a thorough analysis to understand your day-to-day situation. We work hand in hand with you to form an accurate picture of your process and to define the goals we will work toward.
02
Identify your strengths and weaknesses. After the analysis, we will be able to give an honest assessment of what you do well and what areas you need to work on. We always listen to your feedback during this process, so we can work together to find a solution.
03
Make a plan to achieve your goals. Once we understand the situation, we make a plan and a timetable for achieving the goals. This is the time for careful planning and strategizing to find the best way to get to the goal line.
04
Implementation of the plan. We work the plan, adjusting it wherever necessary, but always working toward a successful end result.
Our Team
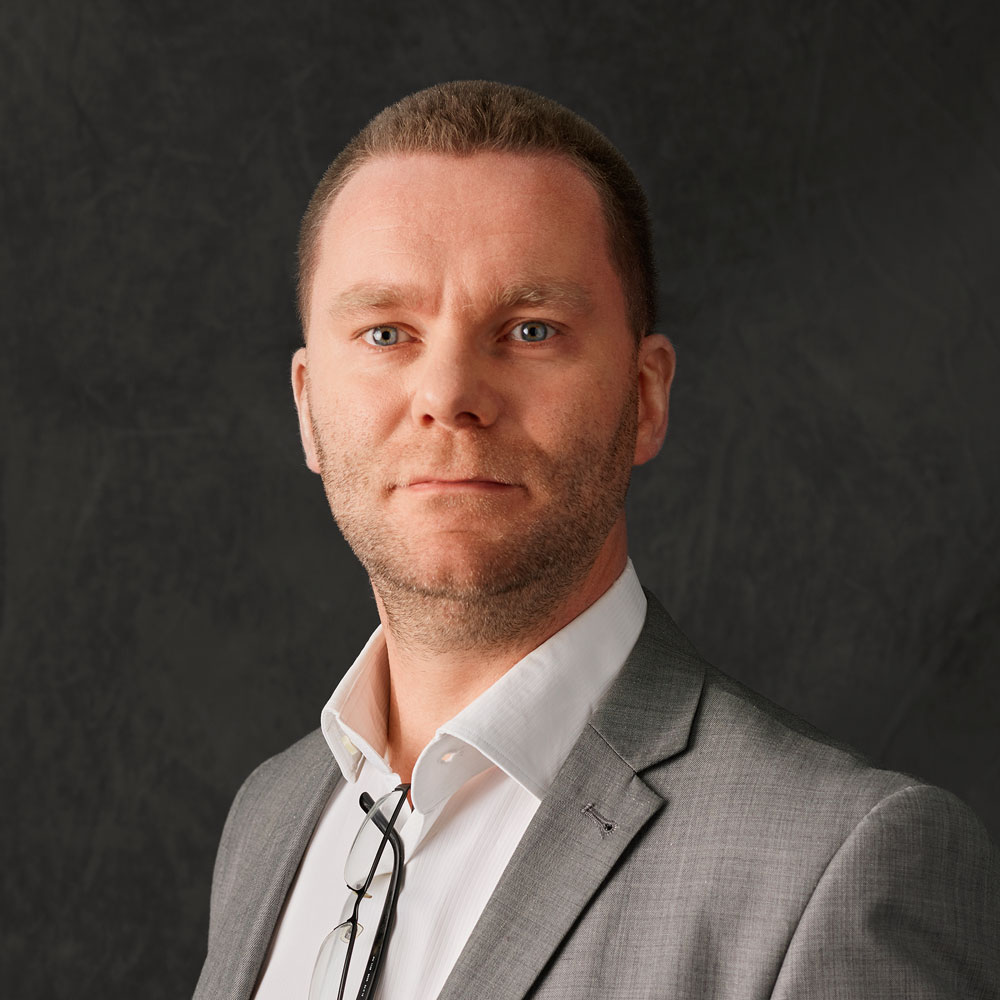
Robert Kohl
Founder and CEO
Robert Kohl, our Founder and CEO, has had a distinguished career in the printing industry, starting with a publishing company he founded when he was only 18. He went on to work for such industry leaders as Agfa, Kodak and Esko, and gained experience in areas like printing, IT, quality assurance, and packaging. He has developed products and companies in the industry, and is now guiding frozentraffic to success in packaging prepress workflow management. He lives with his girlfriend and his four cats in Bavaria, although they (girlfriend and cats) have no expertise in the printing industry – as far as he knows. His two children are studying in Europe.
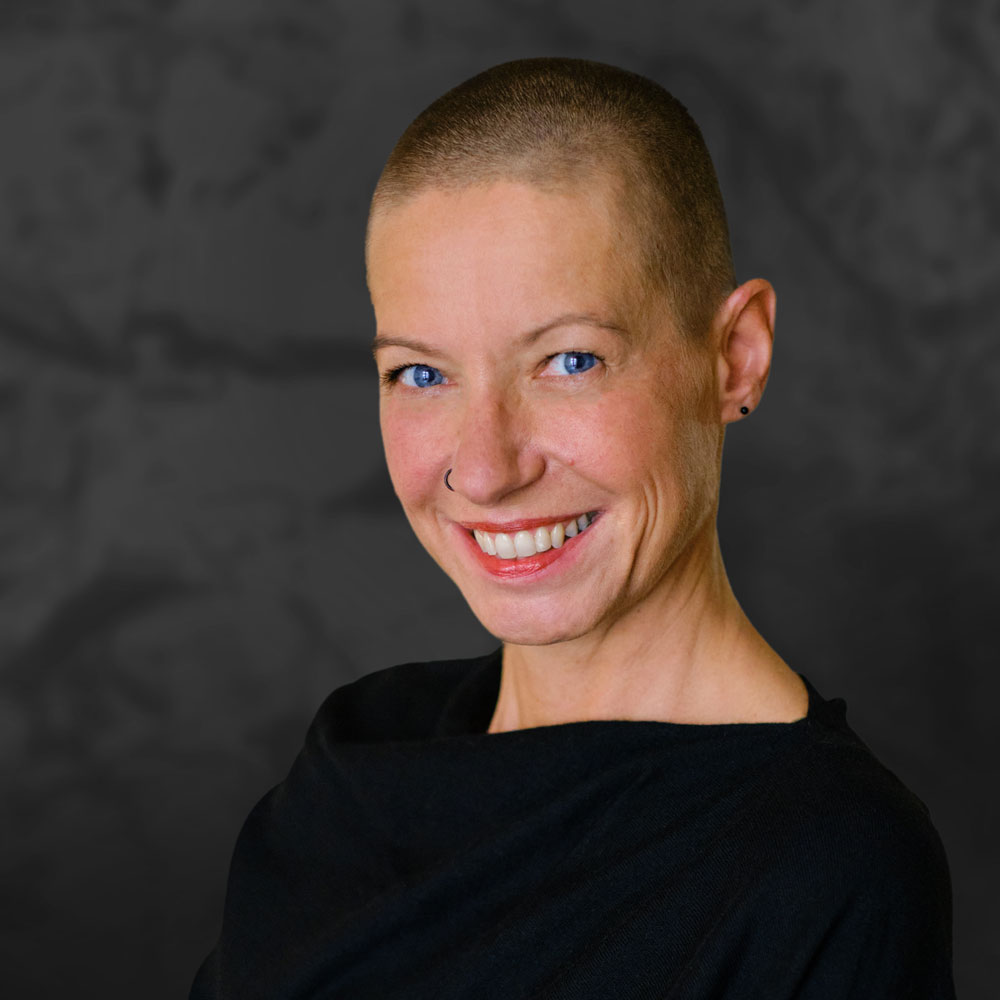
Christina Kerkenrath
Prepress specialist
Christina has many years of experience as a graphic designer, which helps her to understand the perspective of the end user of printing services. At Frozentraffic she specialises in workflow management for customers. She works closely with them to understand their needs, building trust and working with the customer’s production team to find the best way to optimise the prepress process. In her free time Christina takes piano and boxing lessons, and says she enjoys the challenge of learning new skills – although she thinks learning to play Bach is going to be a lifelong challenge.
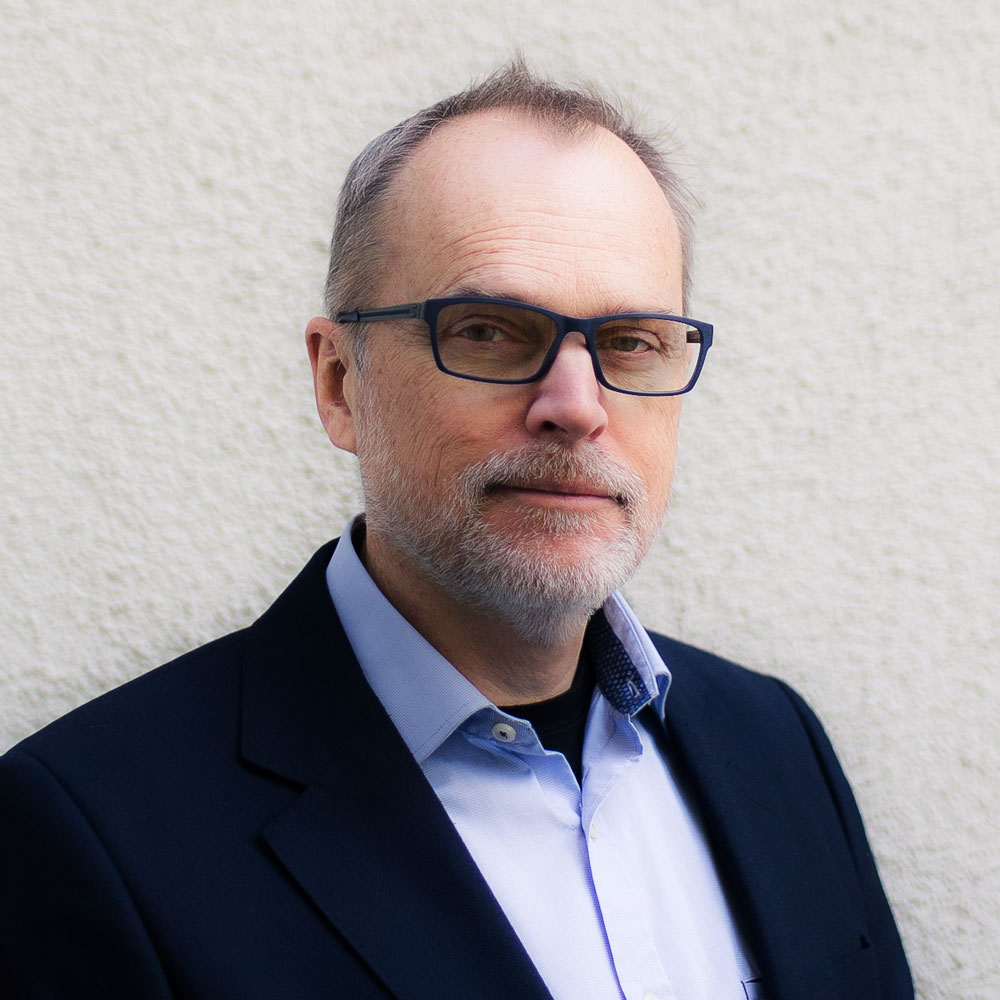
Erol Sener
ERP specialist
Erol started out in the commercial printing industry, working for many years in a family business that did pre- and postpress-production. He left that business and went out on his own as a consultant to the packaging and printing industry. Erol’s expertise is in production planning, configuration, and estimating within different ERP systems. With frozentraffic he concentrates on those ERP areas along with prepress integration, workflow systems, mobile warehousing, and more, with the goal of maximising the benefits of an automated prepress for the customer. In his free time Erol travels with his son, who races cars and last year qualified for the Worldwide Challenge in Italy. “I’m the mechanic, not the driver,” he says, but he enjoys the experience and the time he gets to spend with his son.
Our products
Prepress Analysis
- Accurate data analysis
- Inventory and goal setting
- Data creation, control and processing
- Evaluation of current process and targets
- Identify potential areas for improvement
Automation Assistance
- Implementing of digitization processes
- Data control and processing
- Development of a workflow system
- Smooth implementation of measures for improvement
- Integration and validation
- ERP connection; PrePress automation and production integration
Project Management
- Professional organization and structure
- Planning, management and control of the processes
- Transfer of the processes into a project plan
- Fine tuning the plan for your specific goals
- Defining the content, costs, and timeline for the measures
- Transparency and reporting
Support
- An individual contact person
- Ongoing advice throughout the implementation process
- Training and introduction to the system
- Software support and maintenance
- Continuing support after implementation
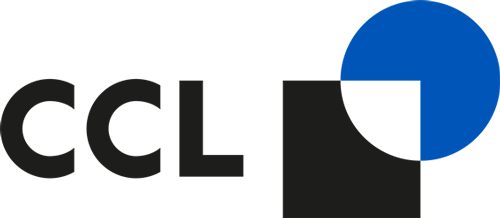
At the start of this project, CCL Hohenems was using Esko’s Automation Engine for its production process, but most tasks were still being done manually by an operator. Frozentraffic launched a workshop to get an accurate picture of CCL Hohenems’s production workflow, including its needs and requirements. After analyzing this information we created a solution for a more efficient, cost-saving process that separated prepress and production orders into two categories. The company liked the solution, so we began to implement it. Our solution automated most of the non-value added steps — e.g., folder creation, approval document creation, project tracking, and transmitting feedback to the ERP.
In addition, we automated more complicated steps like creating a fully automated step & repeat sheet. The result of our solution was that CCL Hohenems saved valuable prepress operator time, increased the exchange of information between ERP and the prepress system, and significantly reduced the amount of error in the process.
– Case Study: CCL Hohenems Systems involved: Esko Automation Engine, Imagine Engine, WebCenter, CCL Hohenems ERP.
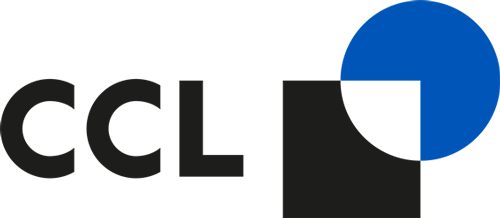
Blindtext…
At the start of this project, CCL Hohenems was using Esko’s Automation Engine for its production process, but most tasks were still being done manually by an operator. Frozentraffic launched a workshop to get an accurate picture of CCL Hohenems’s production workflow, including its needs and requirements. After analyzing this information we created a solution for a more efficient, cost-saving process that separated prepress and production orders into two categories. The company liked the solution, so we began to implement it. Our solution automated most of the non-value added steps — e.g., folder creation, approval document creation, project tracking, and transmitting feedback to the ERP.
– Case Study: CCL Hohenems Systems involved: Esko Automation Engine, Imagine Engine, WebCenter, CCL Hohenems ERP.
Our Publications
Thank you for your interest in our informational material!
You can download our whitepaper directly using the link below:
[Click here to download the whitepaper]
In this whitepaper, you’ll learn how to streamline your prepress workflow, save time, and optimize your processes.
Whitepaper
The four critical pillars to future-proof your
packaging prepress/graphics workflow.
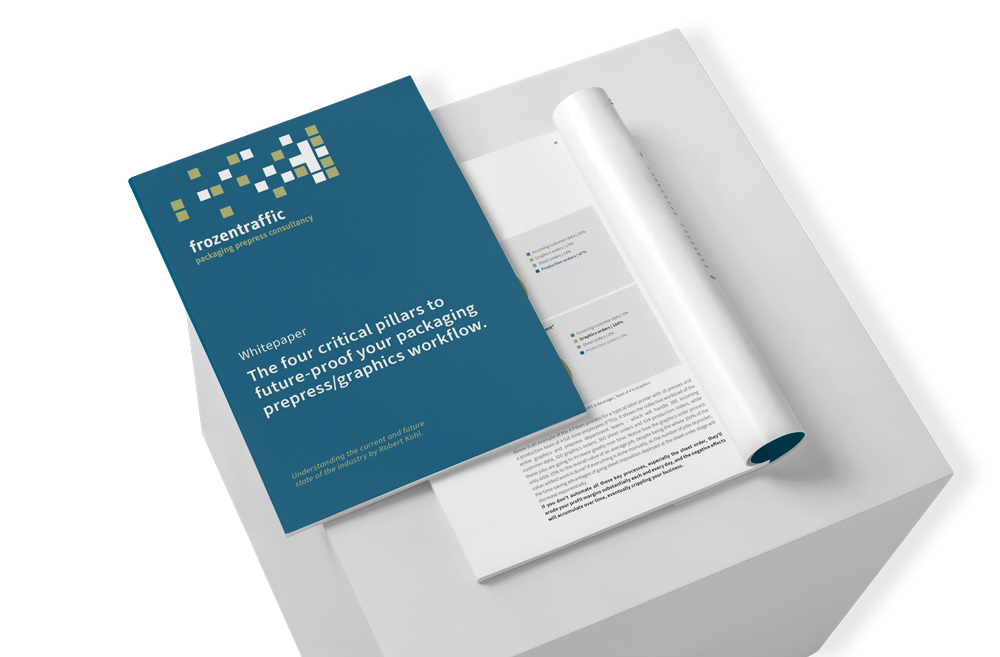
Contact us
Are you interested in optimizing your prepress workflow with frozentraffic? Contact us – we’ll be happy to assist you!